Effective Ways to Prevent Weld Undercut in Your Welding Projects
Effective Ways to Prevent Weld Undercut in Your Welding Projects
Blog Article
Crucial Tips for Welders: Preventing Undercut Welding and Ensuring Stronger Weld Joints
In the realm of welding, accomplishing durable and strong weld joints is the keystone of generating premium job. One usual obstacle that welders usually come across is undercut welding, which can jeopardize the honesty of the weld joint. By understanding the factors that add to undercutting and implementing the right methods and preventative measures, welders can properly stop this problem and make sure the durability and stamina of their welds. Allow's discover some crucial pointers that can aid welders browse this difficulty and raise the high quality of their welding tasks.

Understanding Undercut Welding
Undercut welding is an usual welding problem that takes place when the weld metal stops working to correctly fill the groove and causes a groove-like depression along the weld grain. This problem weakens the weld joint, making it prone to cracking and failure under anxiety. Undercutting can be brought on by numerous variables, including extreme welding existing, high welding speed, improper electrode angle, inaccurate electrode dimension, and poor welding strategy.
One of the primary factors for undercut welding is an inequality between the welding present and the welding rate. If the welding current is expensive or the welding speed is also quickly, the weld metal may not effectively load the groove, leading to undercutting. In addition, making use of an electrode that is too large can lead to a comparable end result, as the excess steel can not appropriately move right into the groove.
To stop undercut welding, welders ought to ensure they are utilizing the right welding criteria, maintain an appropriate electrode angle, select the proper electrode dimension, and technique correct welding strategies. By resolving these elements, welders can lessen the danger of undercutting and produce stronger, much more reputable weld joints.
Appropriate Welding Strategy
Reliable welding strategy plays a critical duty in making certain the top quality and honesty of weld joints. Correct welding method entails a mix of ability, accuracy, and adherence to ideal methods. One essential facet of correct welding strategy is preserving the proper angle and range between the welding gun and the work surface. Welders need to likewise pay close attention to the travel rate and heat input to stop concerns like damaging, porosity, or incomplete blend.
Additionally, a consistent and consistent hand activity is necessary for creating solid and durable weld joints. Welders need to aim for smooth, uniform movements to guarantee also distribution of the weld product. Proper control of the welding weapon and filler product is likewise vital to accomplishing optimum penetration and combination.
Furthermore, managing the warm input and picking the suitable welding specifications based upon the material being bonded are critical consider accomplishing high-quality welds - Preventing weld undercut. Welders must adhere to the recommended settings supplied by welding treatment specifications and adjust them as required based on the particular requirements of the task. By understanding correct welding strategies, welders can substantially enhance the strength and dependability of their weld joints
Picking the Right Electrode
Keeping the right angle and range in between the welding gun and the workpiece is essential when thinking about the relevance of picking the ideal electrode in welding applications. The choice of electrode plays an important function in establishing the top quality and toughness of the weld joint. Electrodes are available in different types, each developed for particular functions and materials.
First of all, selecting the appropriate electrode size is crucial. Thinner electrodes appropriate for welding slim products, while thicker electrodes are better for thicker materials and greater heat applications. Matching the electrode size to the thickness of the workpiece helps attain a well balanced weld.
Secondly, understanding the material structure of the electrode is important. Different electrodes are designed for welding specific products like steel, stainless-steel, light weight aluminum, or cast iron. Making use of the right electrode product makes sure great fusion and minimizes the risk of defects in the weld.
Lastly, taking into consideration the welding placement and method is important when choosing the electrode kind. Specific electrodes are better matched for above or vertical welding settings, while others work well for level or you could try this out horizontal placements. Choosing the right electrode based upon the welding technique improves the overall weld top quality and stability.
Preparing the Base Steel
To make sure a successful welding procedure, what initial actions should be taken when preparing the base steel for welding? Correctly preparing the base steel is important for achieving solid and durable weld joints. The primary step in preparing the base metal is to cleanse it thoroughly to get rid of any pollutants such as rust, paint, dirt, or oil. This can be done making use of a wire mill, brush, or chemical solvents. Furthermore, any existing weld material or residue from previous welding need to be eliminated to ensure a clean surface area for the brand-new weld.
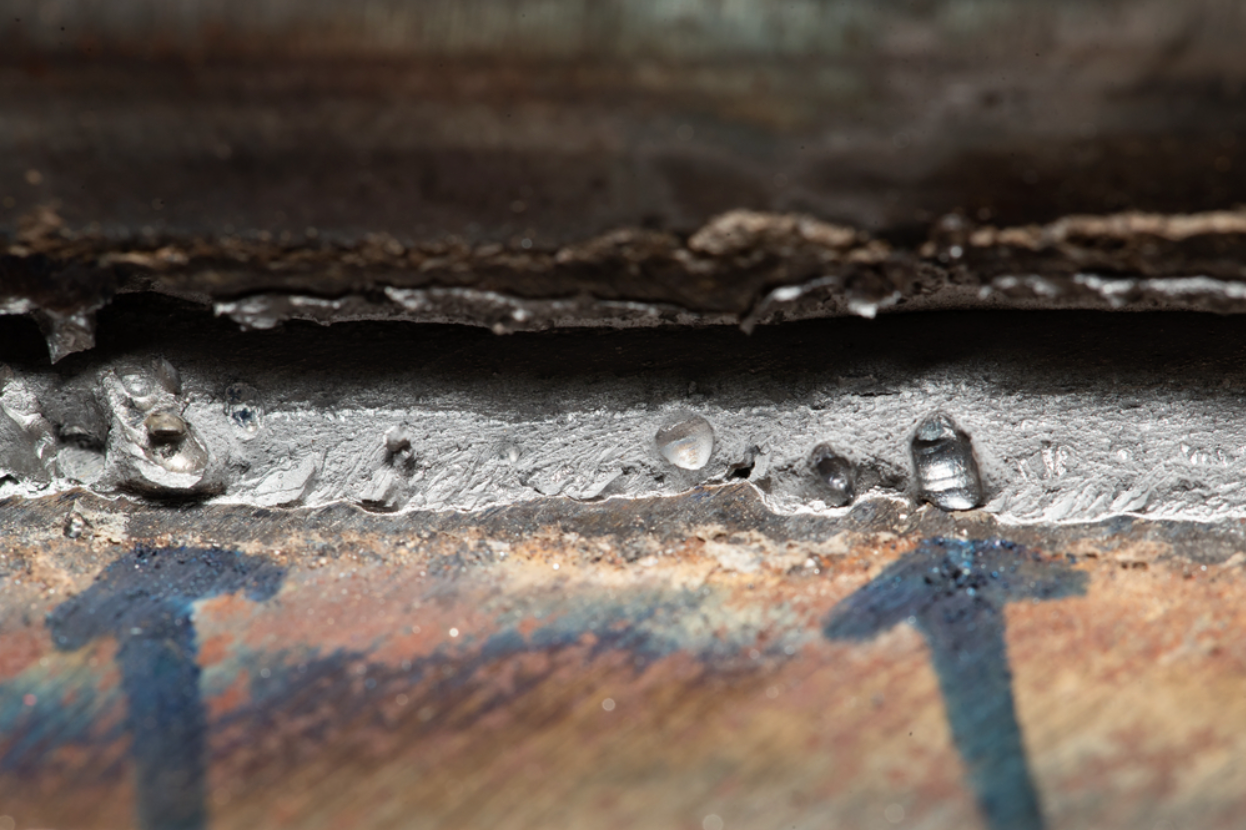
Carrying Out Post-Weld Assessments

After conducting these assessments, welders must contrast the outcomes against industry standards and task needs to guarantee that the weld joint meets all necessary standards. Any kind of variances or inadequacies uncovered during the post-weld examination needs to be immediately dealt with through ideal restorative steps to guarantee the weld's stability. By vigilantly performing post-weld evaluations and quickly resolving any type of issues, welders can promote the high quality and reliability of their job, ultimately adding to the security and long life of the bonded structures.
Final Thought

To conclude, stopping undercut welding and guaranteeing more powerful weld joints need a mix of appropriate welding technique, selecting the appropriate electrode, preparing the base metal correctly, and performing post-weld evaluations. By understanding the sources of undercut welding and implementing the needed precautions, welders can create high-quality weld joints that satisfy sector standards and make sure the structural honesty of the welded elements.
Undercut welding is an usual welding problem that happens when the weld steel fails to correctly load the groove and results in a groove-like clinical depression along the weld bead (Preventing weld undercut). Undercutting can be caused by different variables, including excessive welding present, high welding rate, inappropriate electrode angle, incorrect electrode size, and poor welding method
One of the primary factors for undercut welding is an imbalance between the welding current and the welding speed. If the welding current is as well high or the welding speed is as well fast, the weld metal may not appropriately fill the groove, leading to undercutting.Maintaining the appropriate angle and distance between the welding gun and the workpiece is basic when considering the significance of selecting the best electrode in welding applications.
Report this page